Manufacturing Automation That Fuels Efficiency
Source materials globally and track raw material supplier payments with precision. Plus, you can automate multi-currency transactions, PO matching, and supplier onboarding.
Manufacturing and Wholesale Features
Turn Your Business Into a Lean Machine
Predictable cash flows are essential for your profitability. Our connected solutions across accounts payable, mass payments, procurement, and expenses help you cut costs, mitigate risk, and increase operational efficiency—all without hiring extra staff.
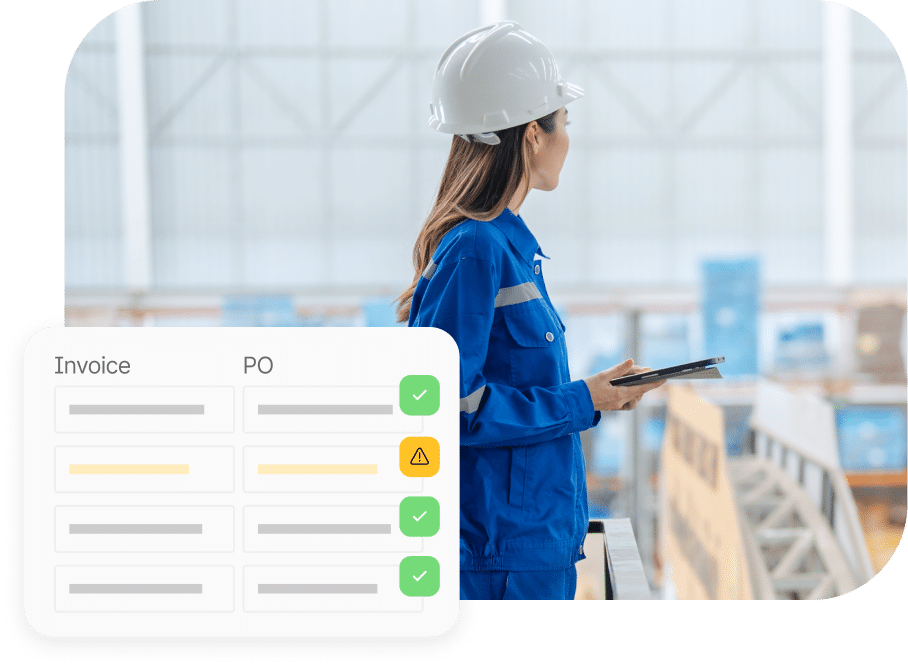
Precision PO Matching
Accurate PO matching to streamline inventory management and boost productivity. Also, eliminate overspending and strengthen financial controls.
Personalized Onboarding
A user-friendly, customizable system for seamlessly bringing new suppliers on board.
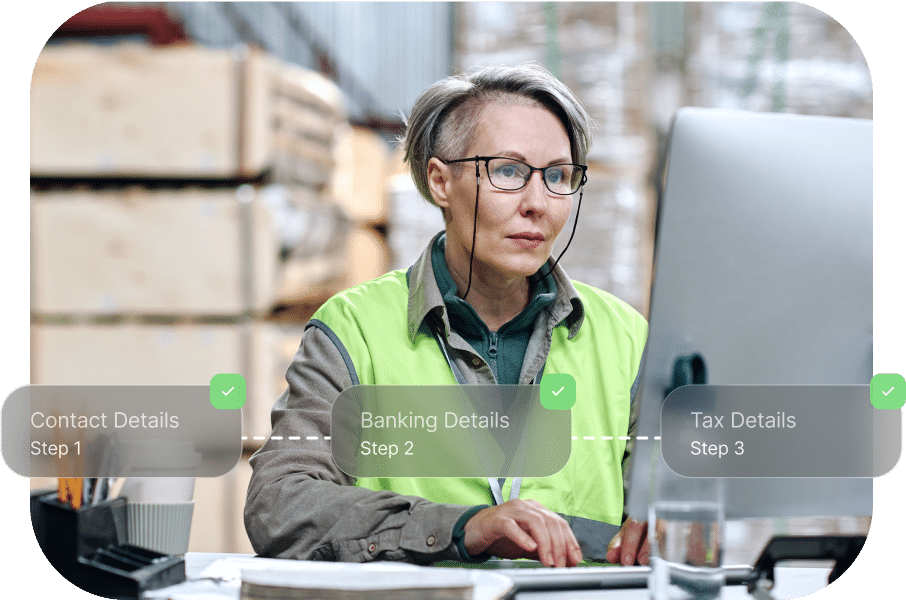
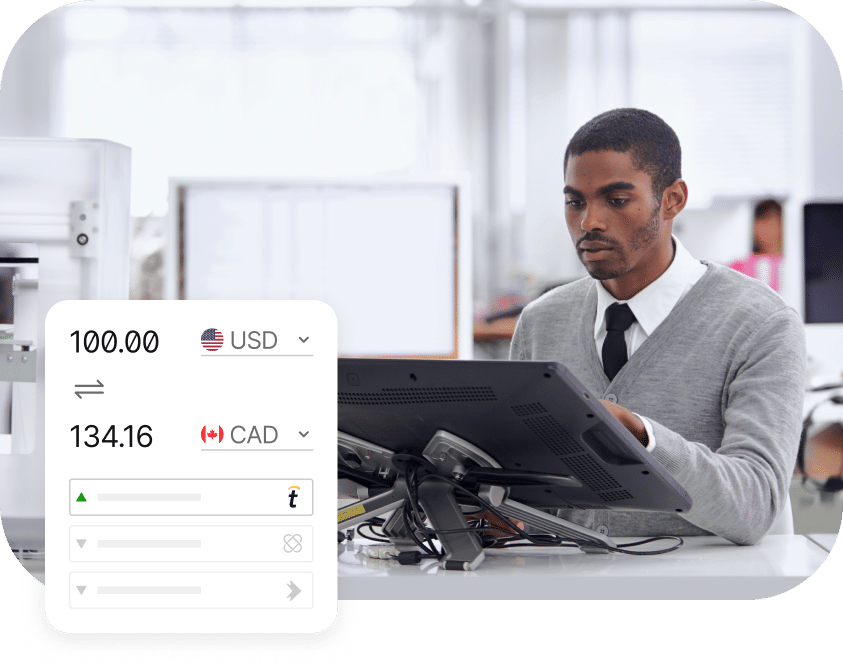
Frictionless Currency Management
Better rates mean you can save on FX fees, while reducing the time and effort required to manage and send payouts in multiple currencies. Plus, payees can get paid in their currency of choice.
Pay Anyone, Anywhere
Pay manufacturers in 196 countries using 120 currencies and 50+ payment methods in a matter of clicks, lowering currency volatility risk.
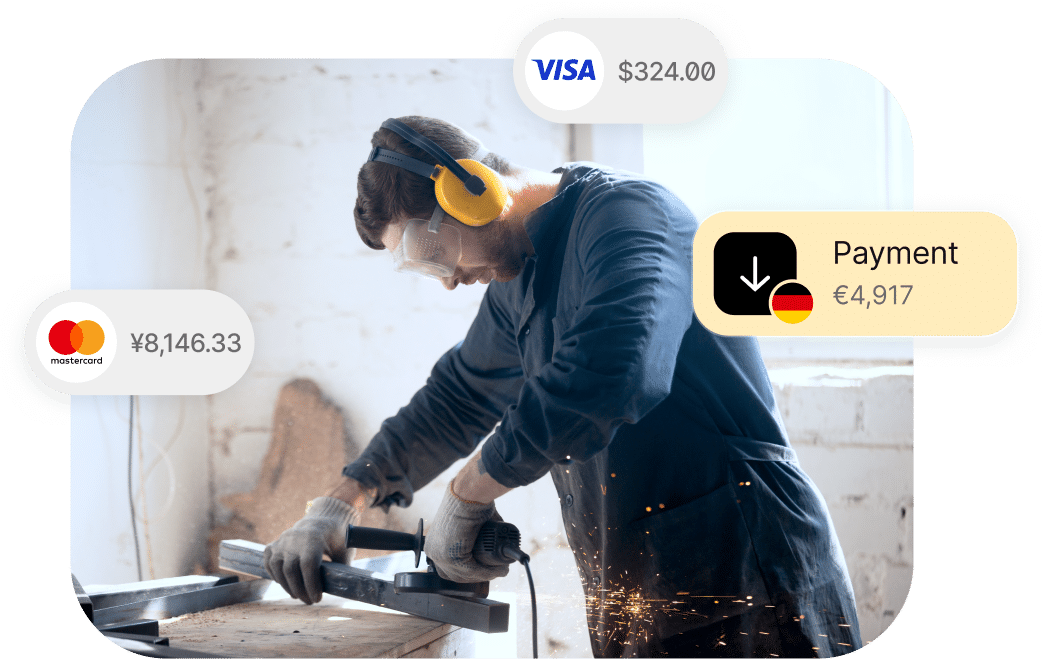
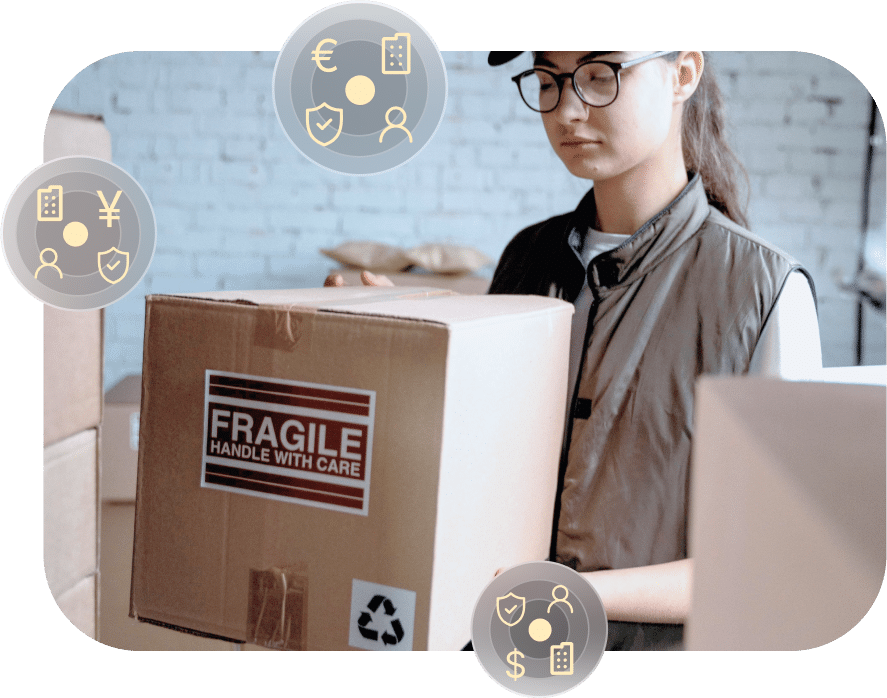
Simplified Multi-Entity Payments
We make it easy to bring accounts payable controls to businesses with multiple subsidiaries, supply chains, and business units.
Integrate With Existing Systems
Connect other systems to your payments engine to increase transparency—including ERPs like NetSuite, Acumatica, Sage Intacct, Microsoft, and Xero.
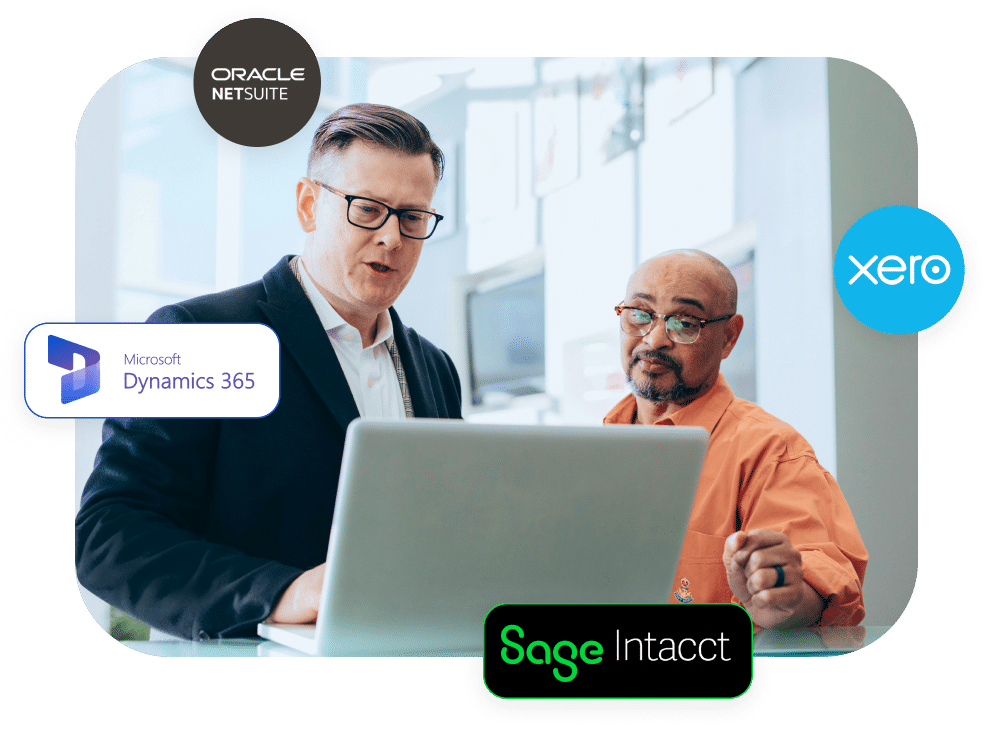
Customer Stories
Don’t just take our word for it,
see what our manufacturing and wholesale customers are saying
Brooklinen
Read how this luxury bedding company managed to shave seven days off its financial close process—error-free.
T3 Micro
Read how this premium hair tool company removed 50% of its manual work without hiring additional staff.
Therabody
Discover how this leading manufacturer of wellness products reduced processing costs and eliminated 60 hours of AP work each month.
Vivino
Find out how the world’s largest online wine retailer reimagined its vendor onboarding and approval process, reducing its multi-country, multi-currency payment process from hours to minutes.
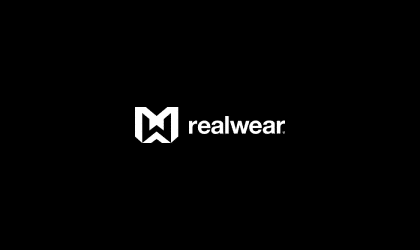
Realwear
Learn how this AI-powered smartglasses pioneer streamlined its payment workload by 20% and cut its financial close cycle in half.
How It Works
Up and running in weeks, not months
Collaborative customer support with customized onboarding to get you operational quickly
Step 1
Plan
Kickstart your success with a comprehensive setup call that reviews your manual AP workflow, outlines the onboarding plan, validates technical configurations, and prepares for training.
Step 2
Configure
Tipalti’s implementation experts set up your hosted portal, create sample payment files, configure payment options and email integrations, and establish ERP integrations using our pre-built solutions.
Step 3
Deploy
In-depth training for AP staff on the Tipalti Hub and the end-to-end AP automation functionalities, ensuring thorough knowledge transfer to turbocharge your successful launch.
Step 4
Adopt
Support user adoption and change management during launch while guiding suppliers through onboarding. Once set, you’ll be ready to execute your first payment run and officially launch Tipalti.
Step 5
Optimize
Continued technical support by phone and email. Tipalti customer success team learns your goals and offers solutions to reach them.
Products
Everything you need to control spend
Tipalti’s connected finance automation suite ensures you get the visibility and control you need across accounts payable, global payments, procurement, and employee expenses to run your business more efficiently and drive growth.
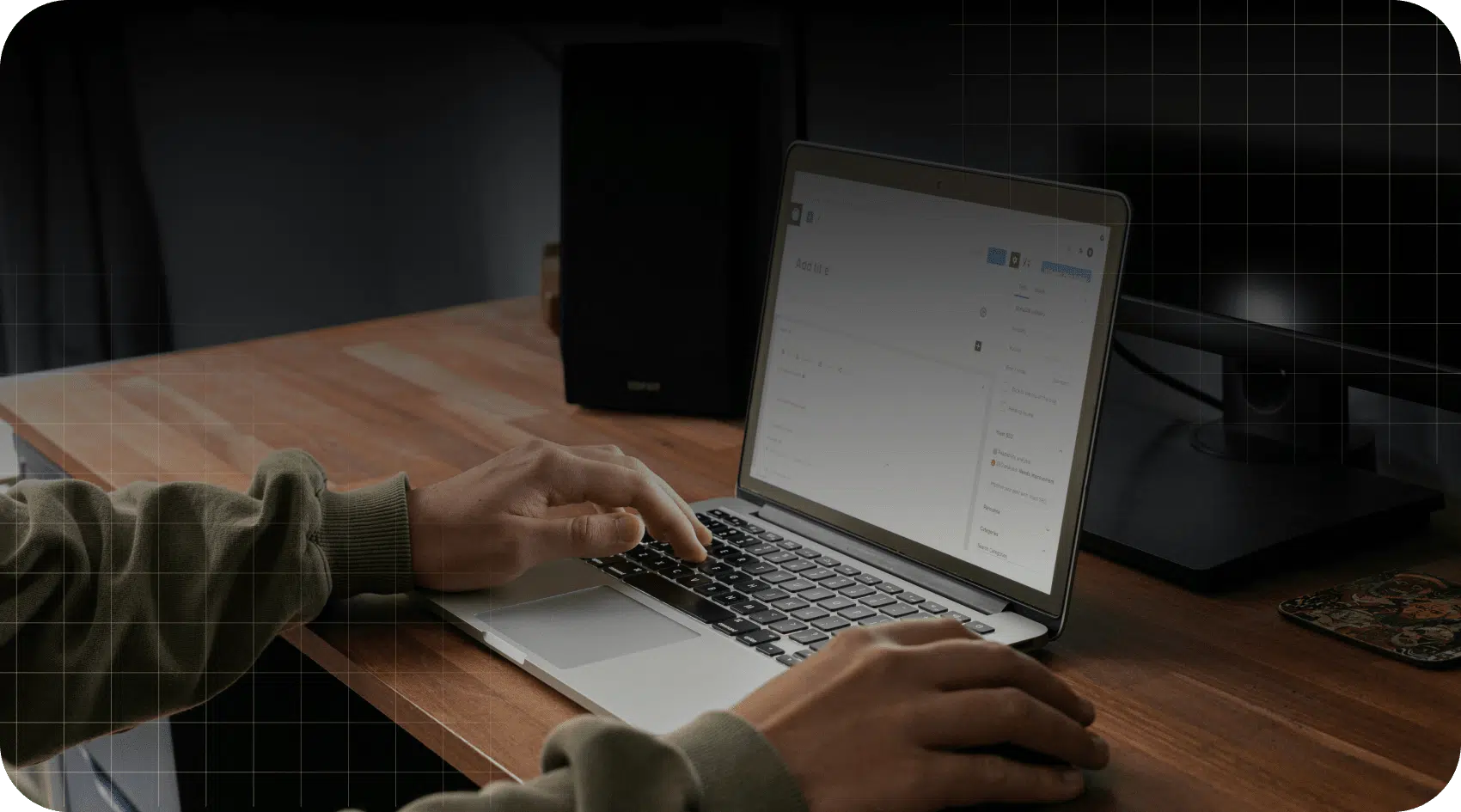
Ready to save time and money?
Book a demo to get started today and take control of your finance operations with Tipalti.
Recommendations
Access All Insights on Manufacturing
Manufacturing Payment Solutions FAQs
What is AP in manufacturing?
Accounts payable (AP) in manufacturing refers to a financial process in which an organisation manages its obligations to pay off short-term debts to suppliers or creditors.
Manufacturing AP involves tracking invoices, managing terms, making payments, and maintaining vendor relationships.
In manufacturing, efficient AP management is crucial—especially when handling large volumes of transactions. You also need intelligent AP automation software to maintain smooth operations within the supply chain, handle discrepancies, and avoid late payments.
How does Tipalti AP automation integrate with existing manufacturing systems?
Tipalti offers a variety of AP automation tools that can smoothly integrate with your existing manufacturing systems.
Integrations include:
ERP Integration
Tipalti can seamlessly integrate with manufacturing ERPs like SAP, Microsoft Dynamics, and Oracle. It can synchronize financial data in real-time, reducing errors and manual entry.
API
Tipalti offers robust API capabilities that enable custom integrations with various MRPs (Manufacturing Resource Planning) systems and other specialized platforms. Ensure all AP processes offer scalability and can be customized to fit specific workflows in a manufacturing business.
Supplier Portal
Suppliers and vendors can upload invoices and track payments through a self-service portal. This portal typically integrates with the manufacturing company’s legacy systems, ensuring instant communication and real-time updates.
File Import/Export
Tipalti allows information to be imported and exported using standard formats like XML or CSV for systems that might not support direct integration.
Can I connect accounts payable with my MRP or ERP system?
Accounts payable can be integrated with various centralized systems, including MRP (Manufacturing Resource Planning) or ERP (Enterprise Resource Planning) systems.
Benefits of integrating accounts include:
- Automated workflows: Streamline invoice management, including approvals, payments, and reconciliations.
- Central data management: Ensure all financial and inventory data is unified, leading to better control and visibility.
- Real-time analytics: Provides up-to-date financial and inventory data, aiding in decision-making.
Improved accuracy: Automate data transfer between systems, reducing the need for manual data entry and human errors.
How can AP automation improve efficiency in manufacturing supply chains?
AP automation will significantly improve efficiency in manufacturing supply chains.
Benefits of AP automation include:
Improved Accuracy
It minimizes human error associated with manual data entry, leading to more accurate financial records, fewer bottlenecks, and fewer disruptions in payment.
Reduced Processing Times
AP automation speeds up the invoicing process and the entire AP cycle. You’ll be assured that timely payments and strong supplier relationships are forged.
Streamlined Manufacturing Operations
Systems with AP automation should integrate seamlessly with other business processes, facilitating smoother operations throughout the entire organisation.
Improved Cash Flow Management
Accounts payable automation provides better visibility into cash flow and upcoming liabilities, enabling AP departments in the manufacturing industry to make more informed decisions.
Optimised Compliance and Audit
AP automation solutions help manufacturing companies maintain accurate audit trails and records, which allows them to comply with financial regulations and approval processes.
What is the accounts payable process in manufacturing?
The accounts payable process in manufacturing typically follows these steps:
- Invoice receipt: The first step is receiving supplier invoices for goods and services purchased. OCR scans invoices for data capture using artificial intelligence and machine learning.
- Verifying invoice data: This is the next step in processing invoices. PO matching involves pairing invoices with purchase orders and other documents.
- Approval workflows: The next step for any AP solution is approvals. Routing invoices for approval from relevant managers or departments is an automated process.
- Payment processing: Invoice automation also includes scheduling and processing supplier payments based on agreed terms.
- Recording transactions: The manual process of entering payment details into the system and reconciling accounts.
Reporting and analytics: Generating reports to analyse cash flow, spend, and supplier performance.
Can AP automation help me better manage my inventory?
Yes. AP teams use automation to manage inventory in the following ways better:
Integrations
Automated AP systems easily integrate with inventory management systems to ensure the accurate, real-time tracking of inventory levels and costs.
Supplier Management
AP automation leads to faster invoice approvals and payments. Faster processing enhances supplier relationships and reliability, which is critical for inventory planning.
Cash Flow
Implementing an AP automation system streamlines payment processes, ensuring more funds are available for inventory purchases. Available funds help maintain optimal stock levels and manage inventory efficiently.
Real-Time Data
AP automation software for manufacturing firms ensures that financial data related to inventory is accurate and up-to-date in real-time. This data aids in more informed inventory management systems.
Forecasting
Tools for AP automation provide detailed insights into past trends and expenses, which helps forecast future inventory needs.